12 Jan 2021 HAVOC IN CHINA SUPPLY CHAIN: This Disruption Is in its Infancy and Is Exacerbated by Repetitive, Chronic Issues Including Chinese New Year Shutdown, West Coast Congestion, Labor Shortages, Longshoremen, Equipment Shortages, Etc.
the coronavirus has wreaked havoc with supply chains from china
By Jeffrey Cartwright, Managing Partner | 6 min read
Headlines have been full for the last year of the disruptions in supply chains in China due to the coronavirus. First, the China-wide shutdown to contain the virus there, followed by the shutdowns in the United States and elsewhere. Then, we discovered that we needed products from China, particularly Personal Protective Equipment followed quickly by China-produced items that are used around the home office or involved with home projects such as puzzles, crafts, re-modeling, exercise equipment, kitchen products, and other items for those now semi-quarantined or working from home. These demand shifts – with many items languishing in warehouses and others out of stock and on backorder – continue as companies shift sources and factories increase capacity to address critical needs. The sorting out of these supply chains will continue for the next few years as this disruption is still in its infancy.
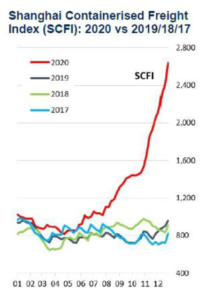
SHOPPING PATTERNS HAVE SHIFTED TO DIGITAL AND RECOVERY OF THE CONSUMER HAS PLACED UNPRECEDENTED DEMANDS ON SHIPPING FROM CHINA TO INDIVIDUAL HOMES
Many consumers have shifted their buying patterns to digital to avoid coming in contact with others in brick-and-mortar retail stores. This has caused great imbalances of inventory as sales are depressed and warehouses remain full of merchandise for some traditional retailers, while the opposite is true for those with a robust digital presence and home delivery such as Amazon, Target.com, Walmart.com, etc.
Then we have the return of demand as warehouses restock depleted inventories and the consumer spends again after months of suppressed demand. All in time for Christmas.
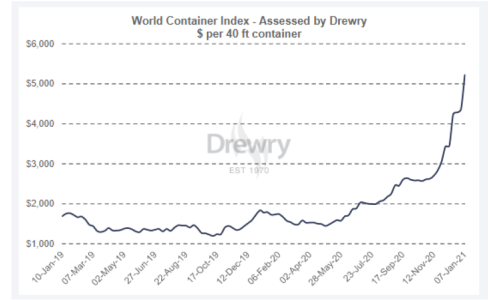
This has caused a massive imbalance in equipment. Some containers are full of product in warehouse parking lots, while other containers are not being returned empty, which means there is a shortage of containers throughout China, Vietnam, Thailand, Taiwan, etc. Space on ocean vessels sells at a premium resulting in a cost increase of 270% from China to the West Coast (spot market) and a 200% increase from China to the East Coast—assuming that there is even space available. Often containers are rolled from one ship to the next in China, incurring a delay of up to a week, which again assumes that the carrier accepted the booking from the factory or importer. Ocean vessels are stacked up again at the ports with as many as 50 ships anchored, waiting for an unloading time at the dock.
Then there is the congestion at the ports where ships are incurring delays of 7 to 14 days to be unloaded and the containers placed on an outbound truck. Inland truck rates have also increased dramatically. If the container needs to be moved by rail to one of the major railyards in Chicago, Dallas, Memphis, or Kansas City, add another 7-to-14-day delay due to lack of available trucking.
In other words, the inbound supply chain from Asia is a mess and has been since October. Even though the Christmas rush has passed, much delayed cargo still needs to be moved. Then we have the upcoming celebration for Chinese New Year which is February 12th. Traditionally, this is a two-week celebration during which time factories close, as many workers travel to their home provinces. Annually, this holiday causes minor delays, and most shippers would have planned for that down period by advancing shipments. This year, given the havoc in shipping, that is not going to happen even with great planning.
Normally, if there are transportation issues due to high seasonal demand, the system returns to normal shortly after Chinese New Year. This year projects balance will not be restored until at least April.
All the above issues on equipment and capacity are further complicated by high absenteeism throughout ocean shipping lines, dock workers, and truck drivers due to the continued spread of the coronavirus – now at the highest levels with lockdowns occurring or imminent.
So maybe later this year in late Q2 or Q3 with vaccines rolling out, things will approach normal.
systemic, chronic disruptions are normal for the china-based supply chain
There will eventually be a return to smoother flow of goods from the massive disruptions of 2020/2021.
However, the underlying causes of the West Coast congestion remain, including too much volume in a short period of time, increased regulation to reduce pollution or improve safety, and the Chinese New Year celebrations each year. In a good year, most companies manage these issues. However, the West Coast back up occurs every few years. 2015 was very painful with a shortage of equipment (chassis and low-emission diesel trucks), combined with a 10-month negotiation of a new labor pact with the longshoremen’s union (with a history of slowdowns and strikes). Note that the next contract date is July 1, 2022.
MEXICO SUPPLY CHAIN ISSUES ARE MINIMAL
Relative to China, there are very minor issues in Mexico’s supply chain. Holiday shutdowns are a week between Christmas and New Year’s Day. Transit times from the industrial area to the border are generally 1 to a maximum of 3 days. Backups sometimes are 4 to 8 hours at the border to the United States. During the threatened shutdown of the southern border, the backup was extended to 2 days.
In short, the Mexican supply chain is far more reliable and considerably shorter, which also results in lower inventory for US companies.
shoreview management advisors and the mexico strategic sourcing alliance
Having built multi-billion-dollar supply chains in China and having built and operated manufacturing plants in Mexico for major US marketing and distribution companies, Shoreview Management Advisors is uniquely positioned to bridge this divide culturally and close the gap in capabilities and execution. We have assembled a strategic alliance of companies that provides an engineering-based approach to sourcing and has 20 plus years of transferring products competitively to Mexico. We develop a thorough understanding with the client of the specifications and required performance of the product. We perform market research in Mexico to add to our list of highly qualified manufacturers. If necessary, we will reverse engineer the detailed product design from samples and create detailed bills of materials. We work with Mexican manufacturing companies in multiple ways to reduce their costs and achieve competitive pricing. If necessary, we source components from Asia and import them into Mexico as part of the total supply chain. We can handle customs and duties, as well as delivery of product to the customer warehouse in the United States. In short, we provide a complete sourcing alternative to China which nearly always results in a lower delivered cost to your distribution centers.
Contact us today to learn what we can do for you.