12 Dec 2023 The Ongoing Trade War and Geopolitical Concerns Have Made Some Companies in Mexico too Comfortable
Nearshoring Will Not Occur without Changes to Mexican Operating Models
Written By Jeffrey Cartwright, Shoreview Managing Partner | 9 min read
There Is a Once in a Generation Change Underway Facilitating Nearshoring to Mexico
As the US – China Trade War reaches its 5th year, and global supply chains face disruption due to the ongoing pandemic, companies are seriously considering Nearshoring as a means to mitigate risks. However, with the recent events such as Russia’s invasion of Ukraine, China’s persistent threats towards Taiwan, and the conflict between Hamas and Israel, Nearshoring has transitioned from being a mere trend to an absolute necessity. The United States is actively reducing its dependence on China for various products. The key question that remains unanswered is whether Mexico will emerge as the primary beneficiary of this shift? If not, what steps can factories take to increase their chances of successfully capitalizing on this opportunity to become new sources of supply for US companies? So far, Mexico has not been at the forefront of redirecting sourcing away from China, as depicted in the graph below:
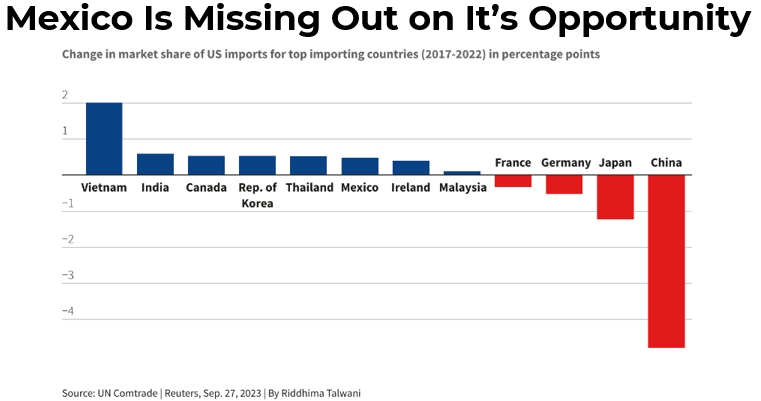
Mexico boasts a multitude of impeccably managed factories, several of which are equipped with cutting-edge, automated technology.
Mexico boasts numerous highly efficient and technologically advanced factories. While these establishments may excel in controlling their production processes, their global competitiveness is not guaranteed. Frequently, these factories rely on longstanding suppliers,
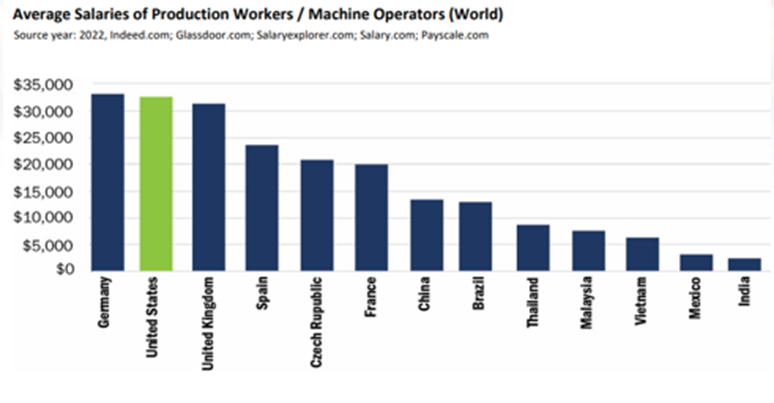
Re-Sourcing of Materials
It would be ideal if the existing factories, which have been relied upon for years, could become globally competitive. One area where there is room for improvement is when it comes to larger quantities of raw materials. In this case, factories should contact producing factories directly instead of purchasing through distributor networks that add a markup for operating costs, thereby reducing profits. These markups can be as high as 25% in many areas. If direct purchasing is not possible, challenging the current distributor with a rigorous bidding process with other distributors can often lead to cost savings. Negotiating experts emphasize that in long-standing relationships where one party has a monopoly, price increases are likely to occur over time.
In-Sourcing a Manufacturing Process (Vertical Integration)
Having been in the metal industry for several years, I have seen that it is possible to in-source several different processes that significantly reduce component cost.
One example, for factories involved in sheet metal, is to invest in a slitter to be able to cut metal to size from master coils, which is less expensive than purchasing a variety of metal widths particularly in pre-cut lengths. Master rolls are less expensive than having some upstream manufacturers slit these roles and then cut them to length. Additionally, the downstream factory will be carrying less overall purchased parts and rapidly converting these into the next production step.
Similarly, other factories purchase tubing of various sizes, both square and round. Investing in a tubing mill allows for comparable savings to slitting and has the same advantage of fewer parts needing to be purchased and stocked.
Both investments eliminate additional factories from the process which eliminates another layer of cost and overhead in the supply chain, directly increasing profitability.
Sourcing of Required New Materials and Components
It is relatively easy to locate a source of materials and components. That is to say to find a source. It is much more difficult to identify several potential sources (best practice is 5 or more) and to conduct a rigorous competitive bidding process to ensure that the selected source is well-qualified and that the price is as competitive with China as possible. Most often the source is in another locale, that will require site visits, a deep understanding of the requirements, and relationship building.
To multinational companies seeking to reduce their dependency on China, it is advisable for Mexican companies to seek alternative sources for components. Failing to secure a crucial component during a crisis could lead to a complete halt in production. An example of this is if Pacific trade is disrupted by armed conflict between China and Taiwan. While Southeast Asia has benefited from the relocation of production from China due to the Trade War, it is important to note that if more than 60% of an Asian factory still relies on parts from China, it does not effectively address the objective of reducing dependence on China, despite resolving tariff issues.
Thinking Beyond the Present to Re-Designing the Product Using Alternative Materials
Mexico has a very strong injection molding industry and is near the global center of resin manufacturing in Houston. China heavily subsidizes manufacturing of steel and aluminum. Converting components made from steel to molded plastic may not only reduce the reliance on China but may also reduce product costs. Companies that have done so report overall cost savings of 25 to 50%. There are over 25,000 different engineered resins plastic materials, and many of these have performance properties that are equal or superior to steel in such things as resistance to impact, corrosion, and heat. While these materials may at first appear to be more expensive than steel, they generally have a 50% lower weight which means the piece cost can be lower. Injection molding is capable of producing complex and geometrically variant components in a single step at higher speed and throughput than metal operations. Consolidating separate metal parts in a single injection mold eliminates several time-consuming manufacturing steps including grinding, welding, or other modes of fastening parts together. Volumes need to be sufficient to pay for tooling, but then injection molded tooling also has a significantly longer life than metal stamping or casting tooling.
Tesla and Toyota are utilizing high-pressure die casting machines that inject molten aluminum into casting molds. This “Giga casting” has the advantage of significantly reducing the number of parts. Tesla has successfully reduced parts from 171 parts to 2 parts for some of its vehicles. Toyota reports a reduction in processing time from 3 hours of labor to 3 minutes or a 98% reduction in labor for 86 parts.
Mexico boasts a robust injection molding industry and is conveniently located near the global hub of resin manufacturing in Houston. On the other hand, China provides heavy subsidies to produce steel and aluminum. However, businesses can potentially alleviate their reliance on China and decrease costs by transitioning from steel components to molded plastic. In fact, companies that have made this shift have reported overall cost savings ranging from 25 to 50%.
The remarkable aspect of this transition lies in the wide variety of over 25,000 different engineered resins and plastic materials available. Many of these materials possess performance properties that are on par with, if not superior to, steel in terms of impact resistance, corrosion resistance, and heat resistance. While these materials may initially seem more costly than steel, their average weight is 50% lighter, resulting in lower piece costs.
The injection molding process has the capability to produce intricate and varying components in a single step at a faster speed and higher throughput than traditional metal operations. By combining multiple metal parts into a single injection mold, manufacturers can eliminate time-consuming steps such as grinding, welding, or other methods of fastening parts together. Additionally, injection molded tooling boasts a significantly longer lifespan than metal stamping or casting tooling.
Notably, both Tesla and Toyota are making use of high-pressure die casting machines to inject molten aluminum into casting molds. This innovative “Giga casting” technique offers the advantage of greatly reducing the number of parts needed. Tesla has achieved impressive results by reducing parts from 171 to just 2 for certain vehicles, while Toyota has achieved a drastic reduction in processing time, reducing labor from 3 hours to a mere 3 minutes. This equates to a staggering 98% reduction in labor for 86 parts.
Many Factories in Mexico Need to Reduce Cost of Raw Materials and Components to Become More Globally Attractive
While Mexico has benefitted from Nearshoring, relative to the potential it has seriously under-performed. At times, the final cost is significantly higher than other low-cost countries in Southeast Asia. To accelerate the Nearshoring trend, many factories need to challenge their existing supply chains, materials, and processes to breakthrough to a new level of cost efficiency. US executives considering changing sources of supply still must consider the Total Cost of Ownership as the top factor in making changes.
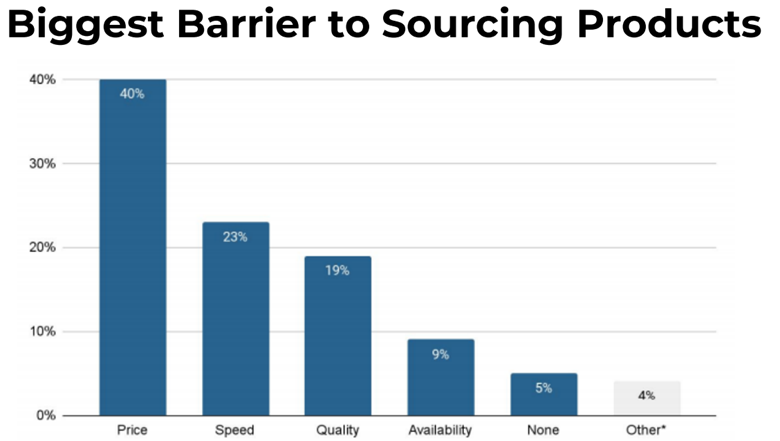
Additionally, every factory would like to produce more of the same things that they have been producing. The products that have been sourced by the US from China are not the always the products that are currently produced in Mexico.
Those Mexican factory owners looking to significantly grow their business should tour US retail stores and imagine the potential of producing some of those items in their factories. Many factory owners have great core competencies, but they need to expand their vision and think as to how they can broaden their capabilities beyond automobiles, aerospace, or medical devices which are the largest manufacturing segments in Mexico.
Given that the total number of light vehicles sold in the US has been declining over the last 20 years, plus the move towards Electric Vehicles from Internal Combustion Vehicles requires 30% less total labor, added to the efficiency gains of Giga casting, and then finally the latest United Auto Workers contracts with the Big Three automobile companies which was about wage and benefit increases along with guarantees of job security in the US factories, it may be that the Mexican automobile industry will become smaller over the next decade. Companies which are dependent upon exports of automobiles and automobile components to the US should seriously consider converting a portion of their capacity to other product lines which have been principally imported from China.
Transitioning from being the factory of the world to a more regional manufacturing strategy will have its challenges, but the rewards will be great and enduring for decades.
Mexico’s underperformance in Nearshoring, despite its potential, is a cause for concern. In some cases, the costs incurred are much higher compared to other low-cost countries in Southeast Asia. To accelerate the trend of Nearshoring, factories must reevaluate their supply chains, materials, and processes to achieve greater cost efficiency. US executives who are considering changing their sources of supply must prioritize the Total Cost of Ownership as the deciding factor.
In addition, factories aspire to produce more of the same products they have been manufacturing. However, the products that the US currently sources from China may not align with the products manufactured in Mexico. To foster significant growth, Mexican factory owners should visit US retail stores and explore the potential of producing similar items in their factories. While these factory owners possess great core competencies, they need to broaden their capabilities beyond the dominant manufacturing sectors in Mexico, such as automobiles, aerospace, and medical devices.
The decline in US sales of light vehicles over the past 20 years, coupled with the shift towards Electric Vehicles and the accompanying reduction in labor requirements, poses a potential challenge for the Mexican automobile industry. Moreover, recent contracts between the United Auto Workers and the Big Three automobile companies address wage and benefit increases, as well as job security guarantees in US factories. These factors may lead to a smaller Mexican automobile industry in the coming decade. Companies heavily reliant on automobile or automobile component exports to the US should seriously consider diversifying their product lines, which have traditionally been imported from China.
Re-Sourcing to the US (Re-Shoring) or to Mexico (Near-Shoring) has its difficulties and requires significant resources. Shoreview Management Advisors is of value to both Mexican factories looking north for growth opportunities and for US companies looking for a reliable, cost-effective source of products. For the last 5 years, Shoreview has been focused on Nearshoring from China to Mexico, having served many clients before the Trump Tariffs and trade war with China. Prior to this latest imperative, Shoreview executives have over 25 years of experience in Mexico in manufacturing and sourcing of products.
Contact us today if you’re serious about exiting China and moving your sourcing to Mexico.